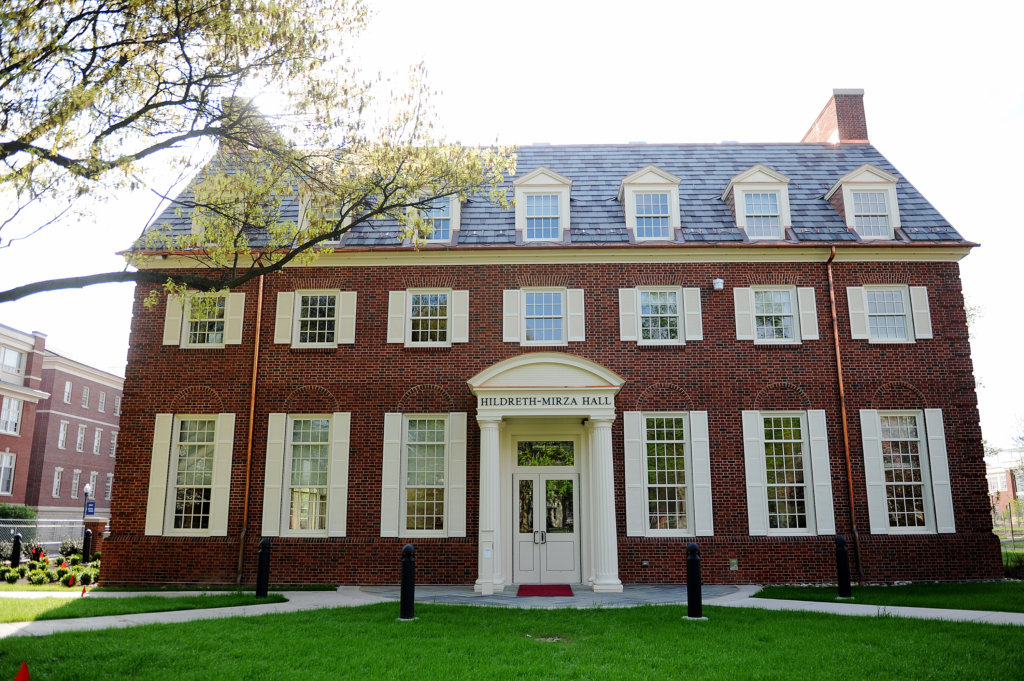
Bucknell University’s Hildreth-Mirza Hall awarded LEED Silver
The new Hildreth-Mirza Hall was certified LEED® Silver by the U.S. Green Building Council. The LEED (Leadership in Energy and Environmental Design) rating system is the foremost program for buildings, homes and communities that are designed, constructed, maintained and operated for improved environmental and human health performance.
Hildreth-Mirza Hall achieved LEED certification for implementing practical and measurable strategies and solutions aimed at achieving high performance in: sustainable site development, water savings, energy efficiency, materials selection and indoor environmental quality.
LEED is the foremost program for the design, construction and operation of green buildings. More than 92,000 commercial and institutional projects are currently participating in LEED, comprising more than 19.3 billion square feet of construction space in all 50 states and more than 167 countries and territories.
Zartman Construction was the general contractor for the $6.4 million addition and renovation to Hildreth-Mirza Hall, home of Bucknell University’s Humanities Center.
Sustainable building initiatives
The renovation and reuse of an existing building reduced the amount of resources needed for the project. Many energy-conserving features and sustainable design elements were also incorporated into the construction process.
Over 50 percent of the construction waste was diverted from landfills and recyclable resources were placed back in the manufacturing process. Wood, asphalt, concrete, brick, metals, cardboard, paper and drywall were all separated out during the process to be diverted or recycled.
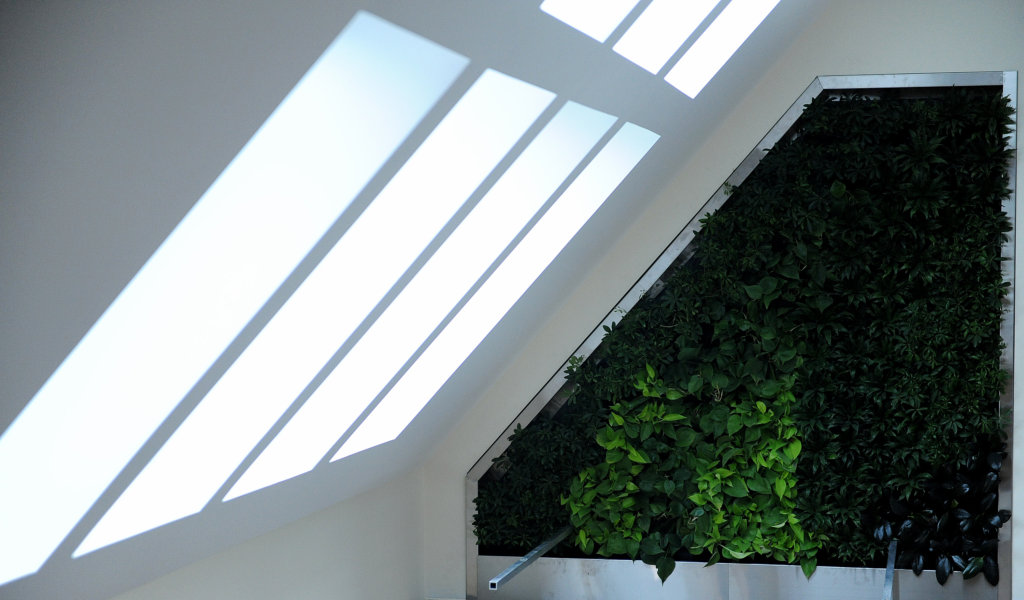
Regional materials were utilized whenever possible, including steel, concrete, brick and drywall. These materials were extracted, recovered or manufactured within 500 miles of the project, which reduced the environmental impacts of transportation along with supporting the use of indigenous resources. More than 18 percent of materials were sourced regionally. And about 16 percent of the buildings materials, including steel, concrete, drywall and carpet, was sourced from recycled content. Seventy percent of the construction wood products were FSC®-certified.
Water usage within the building was reduced by twenty-two percent with the installation of low flow fixtures.
Sensors are used to monitor indoor air quality and during the construction process low VOC-emitting materials were used. The permanent systems will trigger an alarm if airflow values or carbon dioxide levels vary by 10 percent or more from designated values. Occupancy sensors were installed to reduce energy use and the building is a smoke-free facility.
The building’s envelope was improved through the installation of insulation and high performance windows.
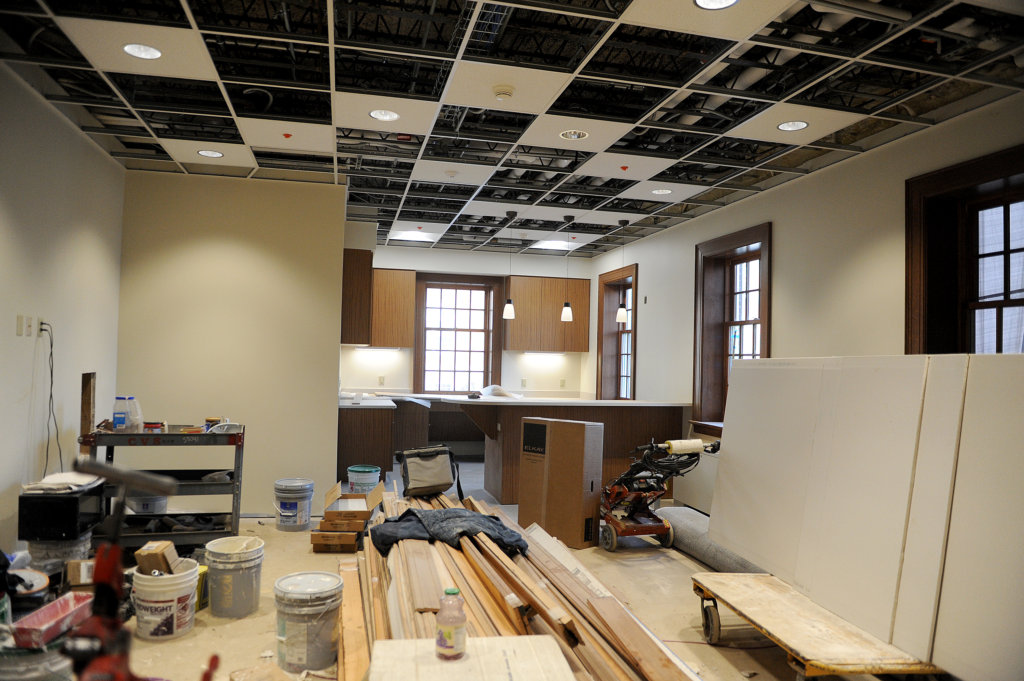
Challenges faced during construction
Due to the limited size of the job site, 35,866 square feet total, the sorting and separating of materials was a challenge. The limited amount of laydown space and ability to have only one dumpster on site meant that many of the materials had to be stored inside the building, constraining an already compact work space.
The compactness of the indoor space lead to extreme congestion during working hours. This made it very difficult to keep the space clean and indoor air quality at a high level. HEPA filtration was used whenever possible to improve air quality.
The installation of the “living wall” in the atrium also proved to be a difficult task due to space constraints. The wall is located on the second and third floors of the atrium and a man lift was utilized for the installation and maintenance of the plants. The lift needed to be able to be maneuvered in and out of the elevator, plus fit inside the elevator for these tasks. There is also a green roof terrace on the second level of the building, the installation of which was delayed due to weather.
The project was also awarded the “Rise to the Challenge” winner by the U.S. Green Building Council Central Pennsylvania chapter.